Fundamentals of Power Electronics Chapter 15: Transformer design22 Determine wire sizes Fraction of window area allocated to each winding: α 1 = 4A 8A = 0.5 α 2 = 1 5 20 A 8A = 0.5 (Since, in this example, the ratio of winding rms currents is equal to the turns ratio, equal areas are allocated to each winding) Wire areas: A w1 = (0.5)(0.5)(0.297) =. Design calculations establish minimum guidelines and requirements for generating electrical calculations on projects. Electrical calculations should be made for all SPU projects that include electrical components and should be filed in the project notebook. Design calculations may be made either manually or by SPU-approved computer programs.

An SMPS transformer becomes apparent at the output of all forward-mode converter. Converters applying the forward, push-pull, half-bridge and full-bridge topologies are typically forward-mode converters. Therefore, calculation of the output inductance employs the equivalent techniques for any 4 of these kinds of widely used topologies. The actual intent behind the output inductor is always to retain power for the load in the period just about every switching cycle whenever the power devices (BJTs, MOSFETs or IGBTs) are switched off. The electrical operation of the SMPS transformer is always to combine the rectangular switching pulses (pulse width modulated signals with changing duty cycle) into DC. The capacitor positioned after the inductor smooths the DC into ripple free DC.
The calculation of the SMPS transformer is pretty straightforward. More often than not, a self-gapped toroid core can be used. Gapped ferrite cores (the types employed for ferrite transformers, eg ETD39) may possibly be accustomed without problems.
The formula for determining the output inductance is:
L(min) = [Vin(max) - V(out) x T(ON) / 1.4 x Iout(min)
Vin(max) = maximum voltage next to the output rectifier within that specific output.
Vout = output voltage.
Toff(est) = anticipated ON time of power device at the maximum input voltage.
Iout(min) = least heavy anticipated load current to achieve that output.

Determined from the above formula is L(min) which is the minimal recommended inductance, below which the core is going to be drained of flux at the least rated load current for that specific output.
Make sure you plan a circuit that permits for functioning without having any load. Unquestionably, you can not replace zero for Iout(min) because that might contribute to an L(min) figure of infinity. And surely, that actually isn’t imaginable, could it be?
Which means that, what you need to accomplish is that you ought to decide upon the very least permissible current.
Work with a resistor load along at the output of the power source in order that should you have hardly any load, this resistor load delivers the bare minimum load.
Iout(min) needs to be significant enough that L(min) certainly is not exceedingly big; it additionally should not be exceedingly massive which may induce excessive power deficits, therefore a negative efficiency, on account of the power dissipation in the output resistor.
Commonly, this resistor is termed a dummy load whose exclusive objective is always to offer the minimal load if there is hardly any other load at the output of the converter / supply of power.
Seeing that we understand the minimum needed inductance, we should comprehend the number of turns to incorporate on our core.
Through the datasheet of the core, you will discover the AL magnitude. This signifies the inductance upon each turns squared:

AL = L/N^2
L will be the inductance and N would be the amount of turns. Implementing M as the argument:
L = √ L/AL
Thus, here is the formula which may be utilized to figure out the quantity of turns when we identify the preferred inductance.
Occasionally you probably will not be familiar with the AL valuation. You possibly will not find out the component spec the core you own thereby unable to identify the datasheet.
No matter what the explanation, it is possible to experimentally identify the AL valuation.

Execute several turns and determine using an L meter, the inductance. After that, measure the inductance for a sets of many different number of turns.
Do it again for all these selected numbers of turns. Therefore, determine the inductance for, as an example, 5, 10, 20, 40 turns after which for each and every, determine the AL value. Obtain the average AL value.
One of the things that can be done is, you might sketch a graph of L against N2. The gradient of the most effective match line could possibly be the AL value. You might also mathematically determine the gradient of the “regression line”. Exercise whatsoever course you realize is the quickest.
At this moment let’s check out a case in point to solve just what you’ve understood until at this instant.
Let’s stipulate that our converter is a half-bridge converter.
The input voltage for the converter will be different out of 150VAC (212VDC) to 250VAC (354VDC). Output voltage from the converter can be 14VDC. The turning frequency is 50kHz.
Transformer primary: 26 turns
Transformer secondary: 4+4 turns
The formula for computing the minimal essential inductance is:
L(min) = [Vin(max) - V(out) x T(ON) / 1.4 x Iout(min)
We will have to evaluate the output voltage with the transformer secondary at 354VDC input, that may be our optimum input voltage.
We’ll believe that the voltage drop as a result of the rectifier diode is 1V. Consequently the typical output voltage within the transformer secondary is 15V. Transformer turns ratio (primary: secondary) = 26:4 = 6.5
Thus, at any time typical secondary voltage is the same as 15V, typical voltage across transformer primary is 6.5 * 15V = 97.5V. In case duty cycle was 100%, voltage across transformer primary could well be 177V (50% the DC bus voltage - consider half-bridge topology). Therefore, the duty cycle is (97.5/177)*100% = 55%.
Average output voltage on transformer secondary will be 15V which has a duty cycle of 55%. Consequently, maximum output voltage is 15V/0.55 = 27.3V, and then there is assumed a diode reduction of 1V. Therefore, Vin(max) is 26.3V.
At optimum input voltage, duty cycle will probably be smallest. This can be any time the off time is going to be the greatest.
We now have determined a duty cycle value of 55% - this is actually the minimum duty cycle number. Since switching frequency is 50kHz, period of time is 20µs. The off period is 0.45 * 20µs = 9µs. Which is our Toff(est).
Let’s stipulate that the particular minimal load is going to pull 500mA current. Using a 14V output and 500mA current, the electricity dissipated in the output resistor will likely be:
P = VI = 14 x 0.5 W = 7 Watts
That is certainly a great deal of power! In case it’s agreeable, by all means employ a 500mA minimum load. If you decide to fetch the minimum load all the way down to 250mA, you trim down power dissipation (above) to 3.5W.
Therefore now we have figured out all the essential variables. Let’s connect these into the formula.
L(min) = (26.3 - 14) x 9 x 10^-6 / 1.4 x 0.25
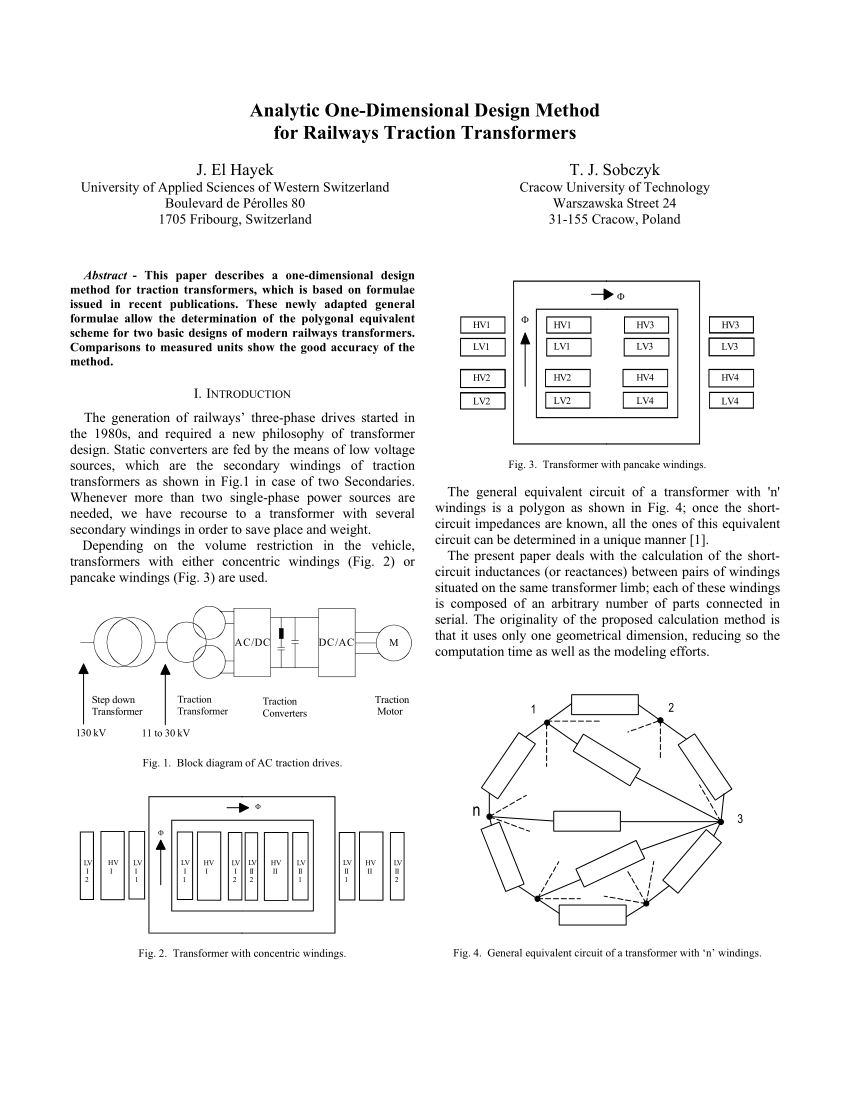
= 316uH
This is often the bare minimum expected inductance. Feel free to use an inductance higher than the minimum number established, considering that, well you determined the minimum essential inductance.
Let’s believe we’ll exploit an inductance of 450µH. Let’s stipulate that we’ve picked out a toroid core with an AL valuation on 64nH per turn squared.
To begin with, the expected inductance is 316µH that could be equivalent to 316000nH.
Therefore the preferred range of turns is:
It can be possibly 70 or 71 turns. This is often for 316µH.
Regarding 450µH:
Transformer Design Calculator
Let's make this around 84 turns.
Transformer Design Calculation Excel Formula
So...now you know How to Calculate SMPS Transformer Turns at home, which you can apply this easy solution in order to determine the necessary output inductance for any converter in which employs the forward, push-pull, half-bridge or full-bridge topology. It’s effortless and also Lets hope I have personally had the opportunity to enable you to comprehend without a doubt. I want to appreciate your feedback and opinions!